Our Director David Kiely and Creative Director Amandine Ringot, recently had the opportunity to travel to Morocco for a behind the scenes tour of the weaving mill that handmakes our textured rugs. In this journal entry, Amandine recounts the insightful and inspiring visit.
In the past decade, I have been fortunate to visit many rug weaving workshops. Humbling and eye-opening, these visits often highlighted the intricate and laborious ways that rugs are made, instilling so much respect for the ancient craft that is weaving.
During our stay in Morocco, I spent two days in-amongst the production, taking photos and gaining a deeper understanding of just how much work and effort goes into each and every one of our textured rugs.
With foundations in the textile industry going back as far as the 1750s, the German owned and managed family business still have their headquarters based in Schwarzach Am Main in Bavaria. Their hand-weaving facilities were established in Rabat, Morocco in the late 1970’s.
It takes a lot of skill and patience to transform a raw material like sheep’s wool into a finished woven rug. From the dyeing, mixing, spinning and felting of the wool to the tying, weaving, and sewing of the finished rug, there is an incredible amount of processes and hands involved in each unique piece. As a valued maker of our textured rugs for over a decade, it was exciting to finally see first-hand the care and commitment of the mill to producing ethical, environmentally sustainable, high quality rugs while showing the utmost respect for their artisan weavers.
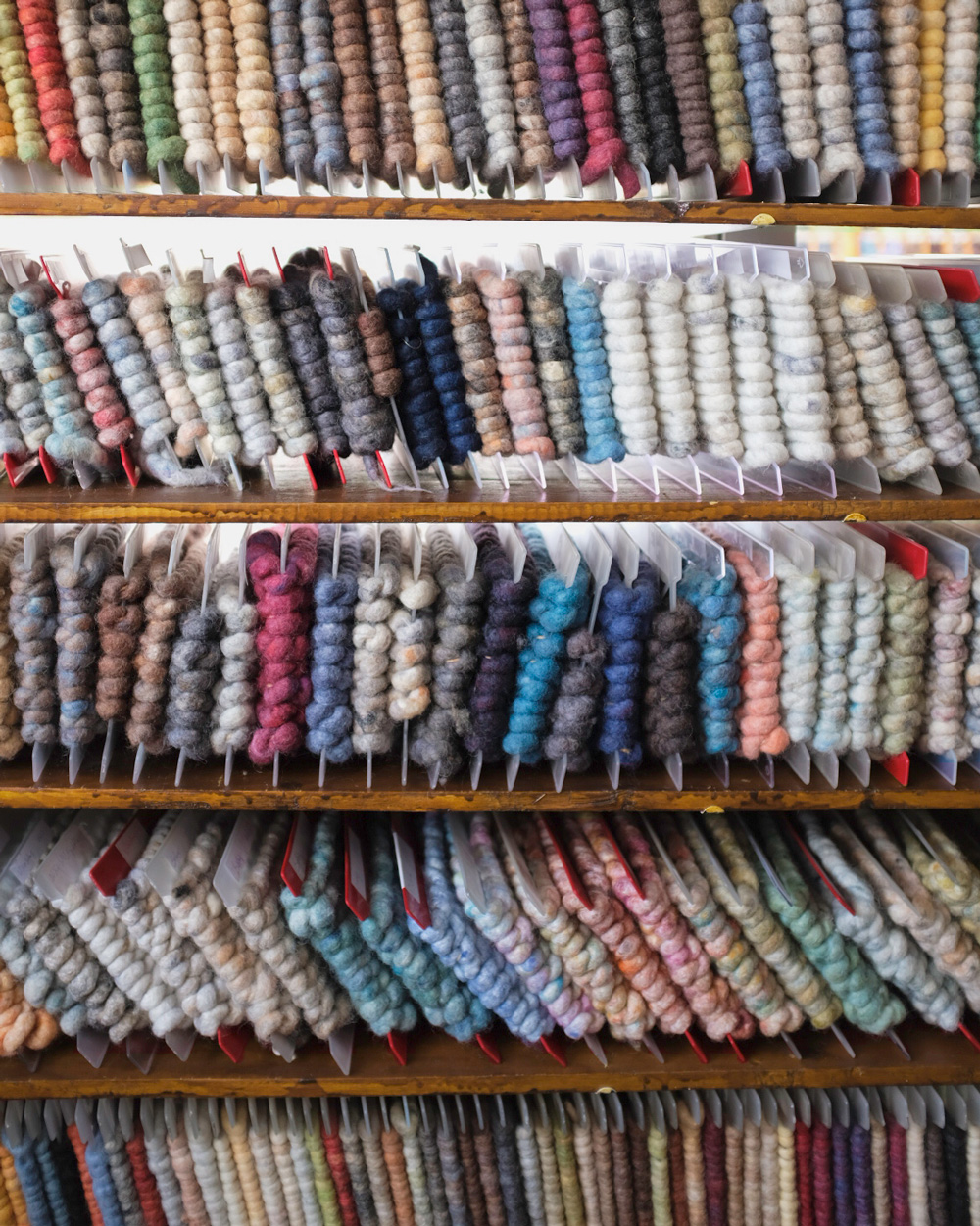
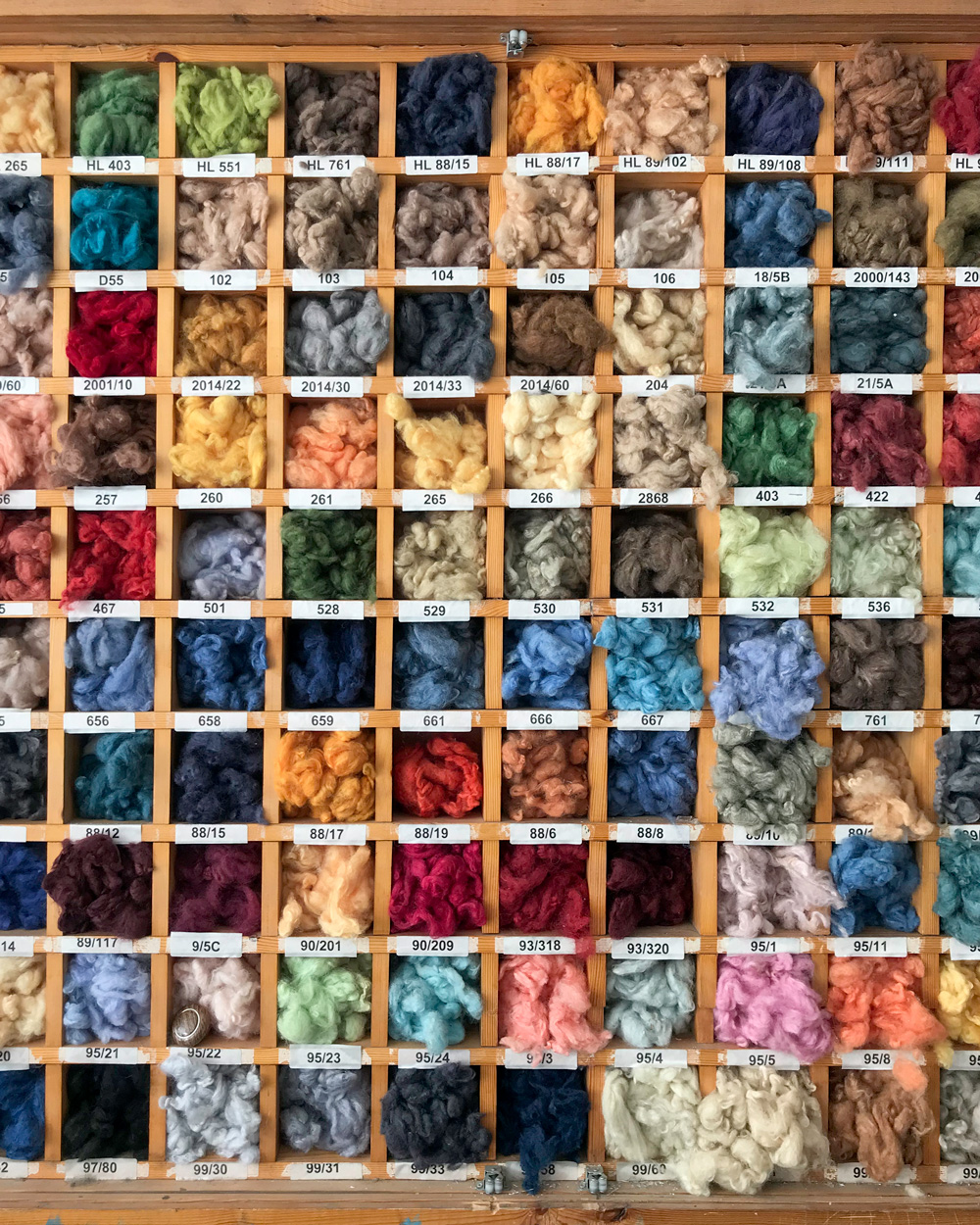
Our first day began with a visit to the wool processing facilities and its extensive wool archive. While gazing at over five hundred coloured wool samples, we learnt that the mill has been keeping records of every single colour that was ever created and used in a rug. All the samples are dated with their production year, some of them dating back to the 1970’s with colours that are still very much on trend.
Crafting a high quality woollen rug starts by selecting the finest yarn available. Sheep’s wool from New Zealand is renowned for its luxuriously soft feel while also being one of the world’s strongest and whitest yarns. It is the only wool used to make our textured rugs as this results in a naturally durable product with exceptionally vibrant and consistent colours.
The first step in the lengthy process of rug making is washing the natural undyed wool several times to remove any impurities. It allows the fibres to loosen, creating ‘flake-like’ pieces of wool which are then dyed in various shades. Using an experienced and creative eye, the Colour Master combines the dyed wool flakes together in specific ratios to achieve the unique mottled yarns we are well known for.
In preparation for spinning the wool into a yarn, the ‘flakes’ are brushed or ‘carded’ to loosen their fibres into long, lustrous strands. These strands are then spun around a jute core to form a thick, textured yarn. The spinning process adds to both the appearance and the durability of the yarn while the jute core acts as a support so it won’t flatten over time.
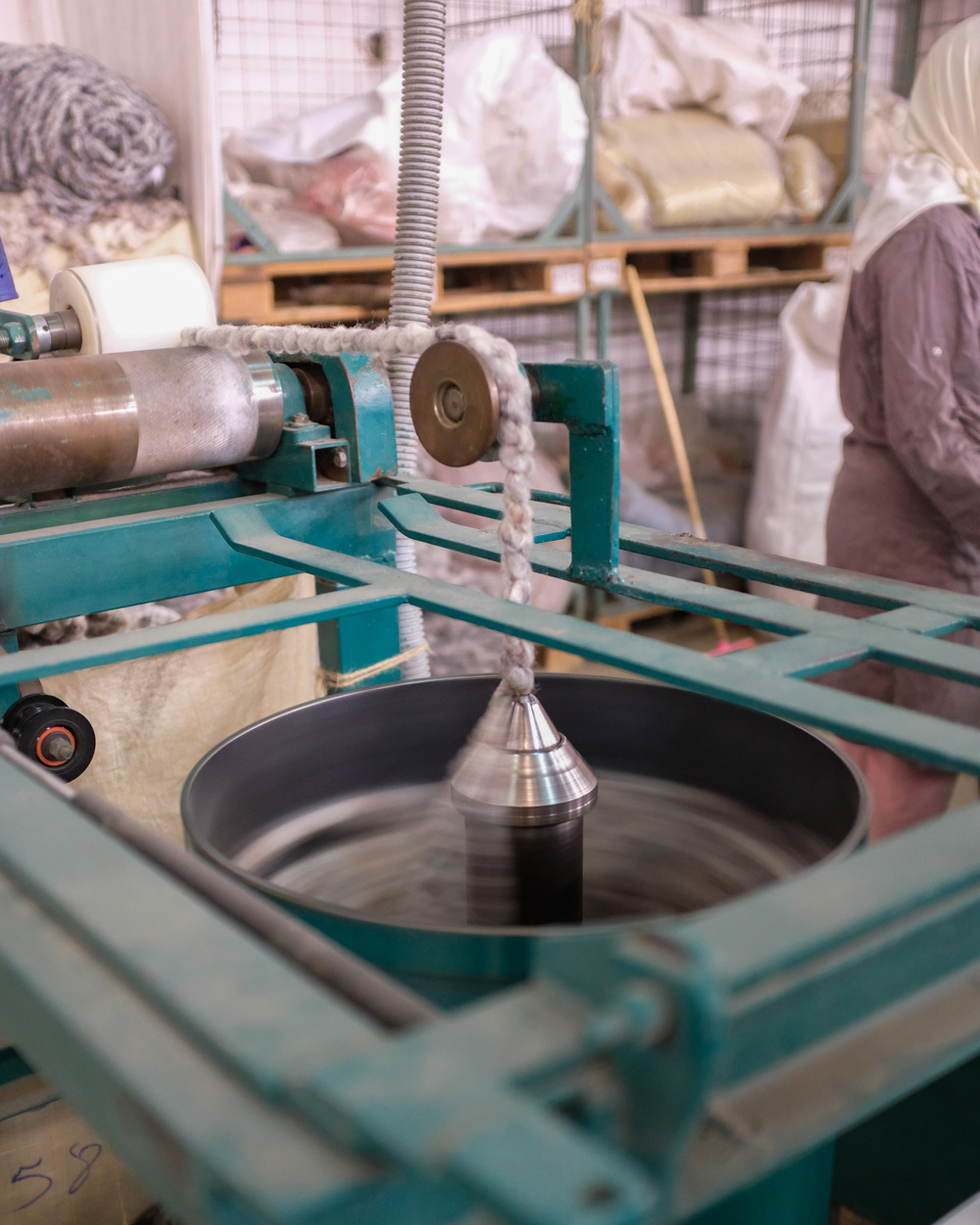
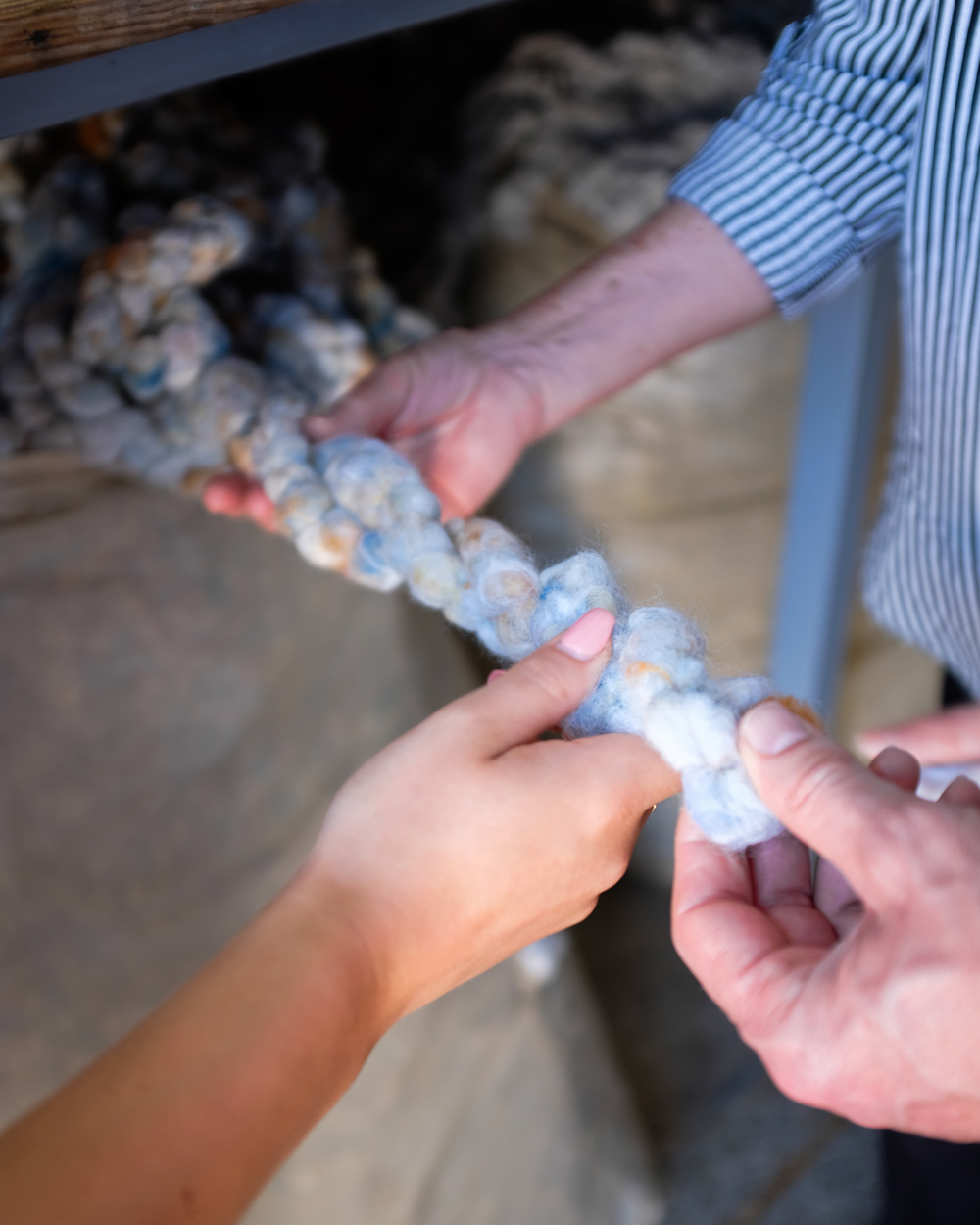
The next step is the felting of the yarn. Using specialised equipment similar to a commercial washing machine, the yarn is exposed to heat, friction and water to shrink the wool fibers and make them fuse together. This process strengthens the surface of the yarn, creating a seal that has a natural resistance to stains and ensuring the rug will not pill or shed over time.
After enjoying the first day at the wool processing facilities, the second day was spent visiting the weaving workshop. The heavy, rhythmic sounds of the looms in action provided the soundtrack for the day as we visited each station to see all the steps and varying weaving techniques involved in the production. Depending on the technique and thickness of the yarn used, each rug takes approximately one to two weeks on the loom before the weaving is finished. It is then tied off the loom and sewed at both ends to create a bound edge or a fringe. A final quality control removes any loose threads or protruding fibres and the final piece is now ready to be packaged and delivered to the happy client.
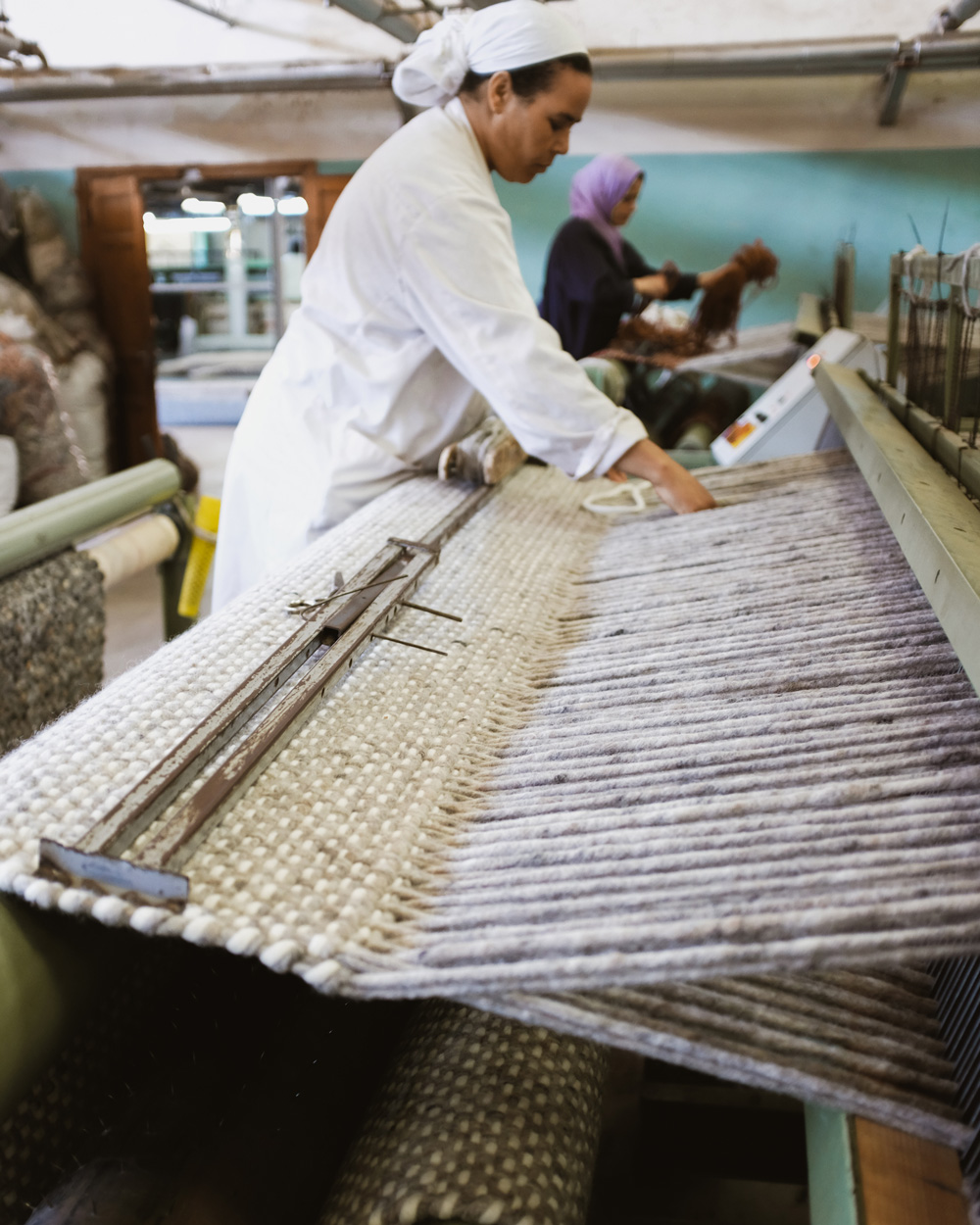
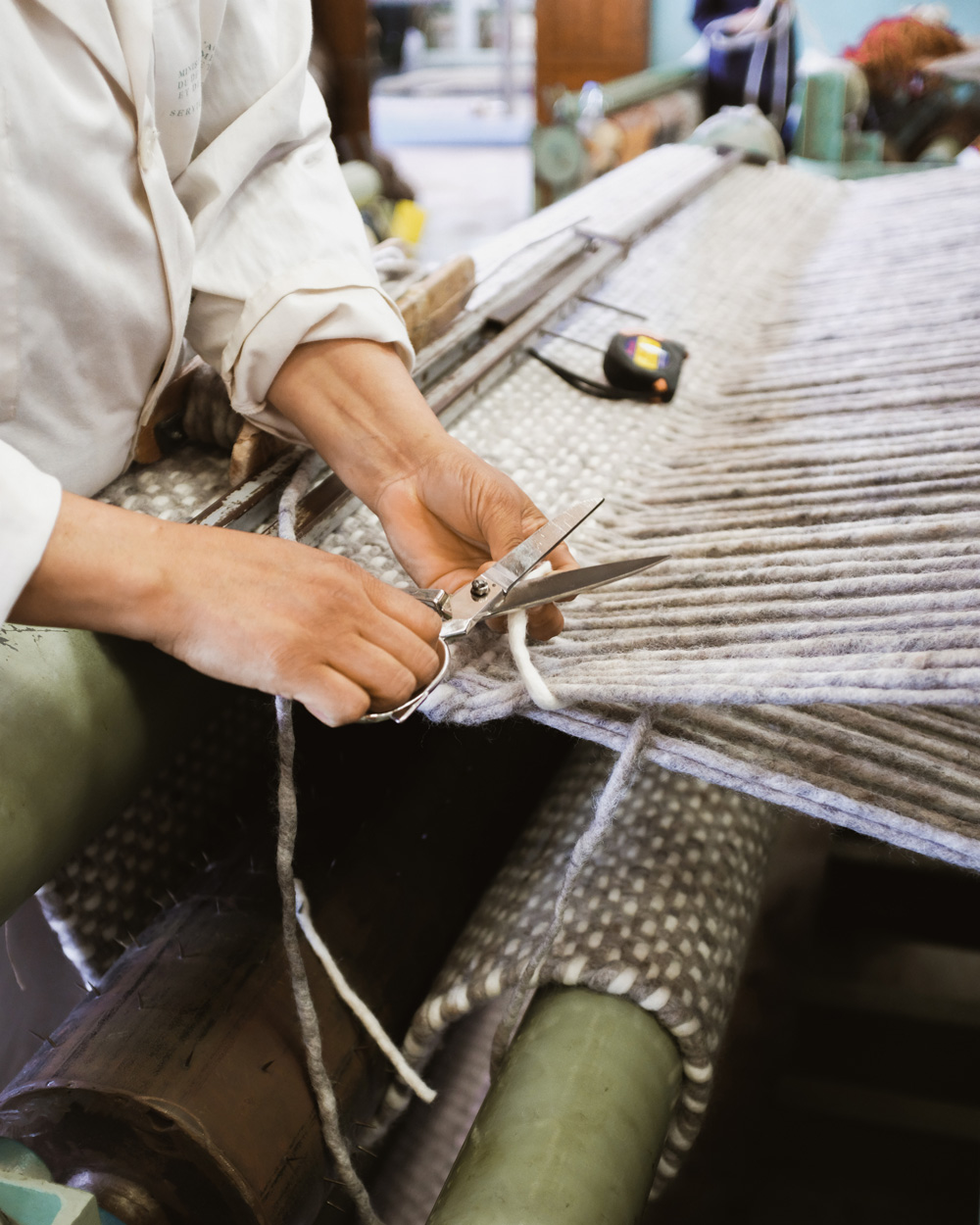
Walking amongst the piles of colourful yarn, witnessing the weavers’ incredible skills and seeing first hand the passion and care of our maker in contributing to a more responsible and sustainable rug industry only deepened our commitment to supporting them. We are honoured to be able to share their story and craftsmanship through their beautiful products, keeping the family’s long standing heritage alive.